Table Of Content
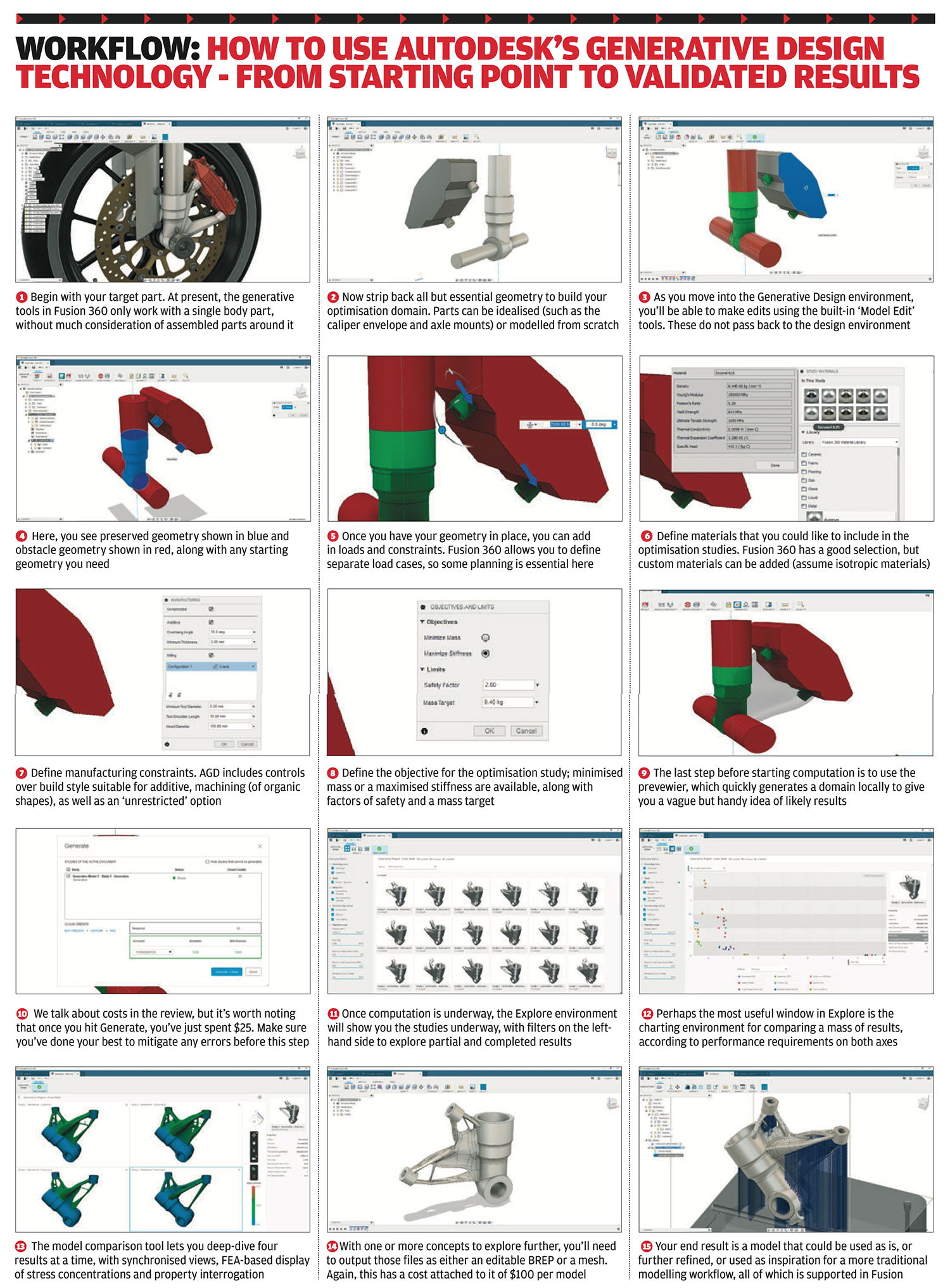
If you add in more materials than are needed or more manufacturing variations, you increase the amount of computation required. Conversely, you’re paying for it, so if you have time, max out your options and see what comes back. The second is that loads and constraints can only be applied to the ‘preserved geometry’ that you have defined; this is absolutely key and might be the cause of some iteration during set-up. In other words, good planning is required upfront before a project begins. When you run the study with the Alternative Outcomes option selected, you will be able to use new features that are described in more detail later, and you may get some additional outcomes on top of the default ones.
A Design Mastermind and His AI Apprentice Arthur Harsuvanakit - Autodesk Redshift
A Design Mastermind and His AI Apprentice Arthur Harsuvanakit.
Posted: Sun, 14 Apr 2024 17:05:35 GMT [source]
Additional tips
Thankfully, the hype train came to the end of the line towards the end of last year, when the Fusion 360 team finally updated the system to include the first variant of this technology as a real-world, commercially available product. After opening the results in the Explore tab, you can identify the outcomes that were generated by Experimental Solvers by the flask icon in the upper right corner of the outcome thumbnail. Inside the Preferences window, find the Preview Features option (5) and then make sure that under the Generative Design tab you have selected Experimental Generative Solvers and Features (6). The green parts are preserve geometries while the yellow part is a starting shape. After opening the results in the Explore tab, you can identify the outcomes that were generated by Experimental Solvers by a flask icon visible in the upper right corner of the outcome thumbnail. Inside the Preferences window find the Preview Features option (5) and then make sure that under the Generative Design tab you have selected Experimental Generative Solvers and Features (6).
Capabilities: Shapes with Voids
One of the characteristics of the new Experimental Solvers is increased variety of shapes. AI can predict demand, optimize inventory levels, and identify potential supply chain disruptions. These systems, as a result, can potentially anticipate shifts in consumer demand and assist in adjusting manufacturing output.
Progressing projects
Again, you have a set of common loads, including forces, pressures and bearing loads. This automatically restricts geometry to this shape – but it’s a shame to nail things down so firmly during early-stage experimentation. At the same time, it can be a challenge to consider your project in this new way and you may need to iterate your problem definition in order to fine-tune it. If you do have an explicit volume inside which you need to work, there is the option to give the system a starting volume. As always, if you have any questions about generative design in Fusion 360, please reach out to us at With your feedback and our continuous improvement efforts in mind, we’re announcing an updated generative design price structure that gives teams of all sizes and budgets a chance to experience its benefits.
The Experimental Solvers feature is a part of generative design which is available to every Fusion 360 user. To open the Generative Design Workspace inside Fusion 360, you need to navigate to the Generative Design option (2) inside the workspace selector (1) in the upper left corner of the Fusion 360 window. With Experimental Solvers and Features, we can get more control over it by constraining allowable displacements. The improved algorithms of Experimental Solvers provide the possibility to remove the material also from the inside if it makes sense for a given model. This allows for faster optimization in some of the cases and produces the shapes that are more optimal from an engineering point of view. To open the Generative Design Workspace inside Fusion 360, you need to navigate to the Generative Design option (2) inside the workspace selector (1) in the upper left corner of the Fusion 360 window.
I will be using this software as:
Grzegorz Borowski is currently a product owner working mainly on generative design at Autodesk. He graduated with a master’s degree in Mechanical Engineering, specializing in Finite Element Method (FEM) simulations. To do this, first open the Preferences window by choosing the Preferences option (4) inside the menu (3) in the upper right corner of the Fusion 360 window.
The final number of outcomes may vary depending on the chosen study configuration; that is, manufacturing constraints, additional constraints like symmetry, etc. Thanks to the continuous work on design divergence, new Experimental Solvers offer up to four additional outcomes on top of the default ones for every study setup. The final number of outcomes may vary depending on the chosen study configuration; that is, manufacturing constraints, additional constraints like symmetry, etc. AI improves product quality and efficiency through data analysis, design optimization, supply chain management, and process automation. Autodesk Fusion exemplifies this integration, offering AI-driven generative design, CAM automation, and future automated drawing capabilities, ushering in a new era in manufacturing. Krystian Motawa graduated with a master's degree in Structural Engineering.
Select verification method
In the traditional generative design approach, we can see the maximum displacement of the generated outcome, but we are unable to directly impact it before the post-processing stage. This means every user of the generative design feature will also see new outcomes with new sophisticated shapes, in addition to the existing traditional solutions. This technology brings new functionalities and delivers forms optimized in a new way, opening doors that have been closed previously. In addition to showing how to use the new technology of generative design in Fusion 360, above all, we will present how the new functionalities empower the new applications using real-world examples. Generative design in Fusion 360 gives you the ability to select multiple manufacturing methods to quickly explore numerous solutions for your design and engineering challenges. All in all, what Autodesk has delivered on here, in its first pass, is pretty damned impressive.
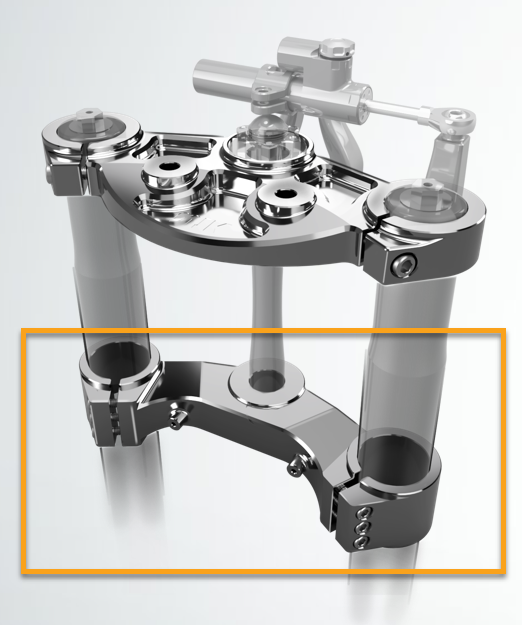
It is also much lighter and has a much lower displacement value than the traditional design. The Experimental Solver brings new possibilities, and you can see the results in the image below. At the top of the image is the design produced by the standard generative design solver. Please note that Experimental Solvers is still a preview feature, which means that some of the new features may not be working with all manufacturing constraints and final outcomes count might be smaller. The full list of supported manufacturing methods is presented later, next to the description of every new constraint.
And then you would still have an enormous amount of processing to do in order to compute it and sift results. As we discussed at the outset, topology optimisation refines a singular form to an optimised state, typically using a singular material. Generative design in Fusion 360 is, by contrast, a platform for experimentation on a much grander scale. There is a natural instinct to compare this set of tools to the more common topology optimisation tools available in other systems (including Fusion 360) – and, at present, the results appear similar in nature. Compared to the ‘all-you-can-eat’ approach to engineering software, this is where things are heading. You might not like it (and I personally have a few issues with it), but it’s a good indication of the adjustments many users will need to make.
Once your load cases are in place, the next step is to start to define the material and manufacturing aspects of the project. One of the characteristics of the new Experimental Solvers is increased variety of shapes. Thanks to new ways of optimization, the results you get for the same study setup can differ significantly in terms of the form while continuing to meet the optimization objectives. This gives you the freedom to choose the design based on its aesthetic values and not only mechanical properties.
Autodesk development teams have been working on capitalizing on these proven simulation solvers as well as the latest technologies in generative design. As a result, a new tech preview feature named Experimental Solver is enabled in Fusion 360. On the other hand, we have generative design in Fusion 360 software — the technology that revolutionizes the engineering world and the ways we design things. Another interesting feature of Experimental Solvers is its ability to create void shapes.
In the standard approach of the generative design solver, the material can only be removed from the outer surface of the model. In most cases, this method provides satisfactory results; however, there are some situations where it is insufficient, and the outcomes that it produces are not the optimal ones. In most cases, this method provides satisfactory results; however, there are some situations where it is insufficient, and the outcomes that it produces are not the optimal ones. The most logical and most optimal solution here would be the shape that has its outer edges preserved and is empty inside. However, up until now, the generative design solver was unable to produce such a shape. The Experimental Solver brings new possibilities, and you can see the results in the image below.
No comments:
Post a Comment